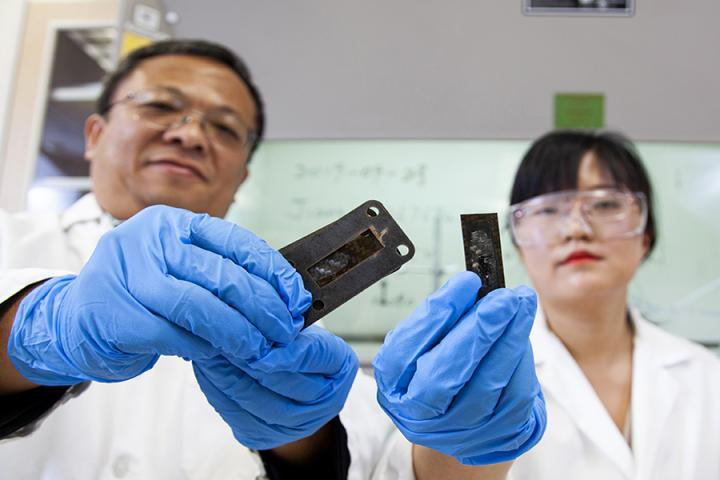
The aerospace industry increasingly relies on carbon fiber reinforced polymer composites to build the structures of satellites, rockets and jet aircraft but the life of those materials is limited by how they handle heat.
A team of FAMU-FSU College of Engineering researchers from Florida State University's High-Performance Materials Institute is developing a design for a heat shield that better protects those extremely fast machines. Their work has been published in the November edition of CARBON .
"Right now, our flight systems are becoming more and more high-speed, even going into hypersonic systems, which are five times the speed of sound," said Professor Richard Liang, director of HPMI. "When you have speeds that high, there's more heat on a surface. Therefore, we need a much better thermal protection system."
The team used carbon nanotubes, which are linked hexagons of carbon atoms in the shape of a cylinder, to build the heat shields. Sheets of those nanotubes are also known as "buckypaper," a material with incredible abilities to conduct heat and electricity that has been a focus of study at HPMI.
By soaking the buckypaper in a resin made of a compound called phenol, the researchers were able to create a lightweight, flexible material that is also durable enough to potentially protect the body of a rocket or jet from the intense heat it faces while flying. Existing heat shields are often very thick compared to the base they protect, said Ayou Hao, a research faculty member at HPMI.
This design lets engineers build a very thin shield, like a sort of skin that protects the aircraft and helps support its structure. After building heat shields of varying thicknesses, the researchers put them to the test.
One test involved applying a flame to the samples to see how they prevented heat from reaching the carbon fiber layer they were meant to protect. After that, the researchers bent the samples to see how strong they remained.
They found the samples with sheets of buckypaper were better than control samples at dispersing heat and keeping it from reaching the base layer. They also stayed strong and flexible compared to control samples made without protective layers of nanotubes.
That flexibility is a helpful quality. The nanotubes are less vulnerable to cracking at high temperatures compared to ceramics, a typical heat shield material. They're also lightweight, which is helpful for engineers who want to reduce the weight of anything on an aircraft that doesn't help the way it flies.
That recognition is helpful for showing the United States Air Force Office of Scientific Research, which partially supported the work, the promise of further research, Hao said.