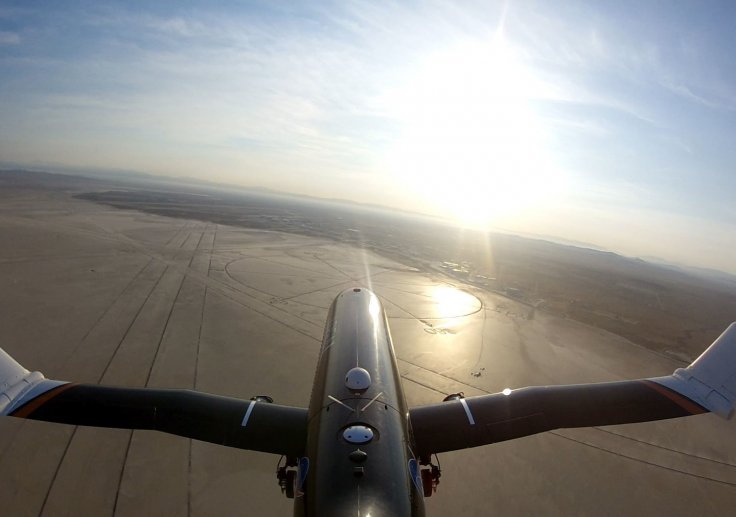
NASA has successfully tested the aircraft which can fold its wings to different angles during its flight. The Spanwise Adaptive Wing project or SAW flight test took place at NASA's Armstrong Flight Research Center in California on January 19, 2018.
The new cutting-edge technology can fold the outer portions of aircraft wings and control their surfaces to optimal angles during flights. It can create multiple benefits to both subsonic and supersonic aircrafts in the future.
Subsonic aircraft used by commercial airlines can fold the wings to increase its controllability. This can reduce dependence on heavier aircraft parts including the tail rudder. It can improve fuel-efficiency of the craft. Pilots can adjust the wings in accordance with various flight conditions like wind gusts and avoid potential air hazards.
The supersonic aircraft which fly above the speed of sound can gain an upper hand by reducing the drag force which acts opposite to the aircraft during its flight.
Matt Moholt, SAW Principal Investigator said, "Through this effort, we may be able to enable this element to the next generation of supersonic flight, to not only reduce drag but also increase performance."
Folding wings in flight technology have been developed from the technologies used in aircrafts including North American XB-70 Valkyrie in the 1960s. Heavy and bulky conventional motors and hydraulic systems were used in these aircraft to fold wings during flight.
An innovatively engineered lightweight nickel-titanium alloy known as shape memory alloy has been used as an activator in the aircraft's vital moving parts. This shape regaining alloy folds the outer portions of an aircraft's wings in flight in place of the earlier heavy hydraulic systems. It weighs 80 percent less than the previous ones.
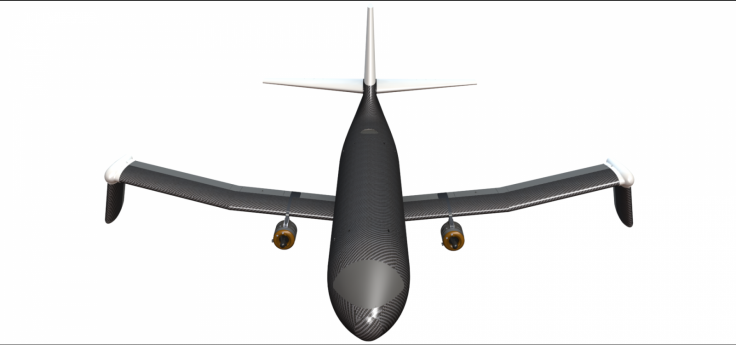
The shape memory alloy works using thermal memory in a tube which functions as an actuator allowing shape changes and regaining of original shape with change in temperature. The test showed zero to 70 degrees up and down folding of the wings during the flight.
Jim Mabe, Technical Fellow with Boeing Research and Technology said, "The performance of this new alloy that we developed between NASA and Boeing really showed outstanding performance."
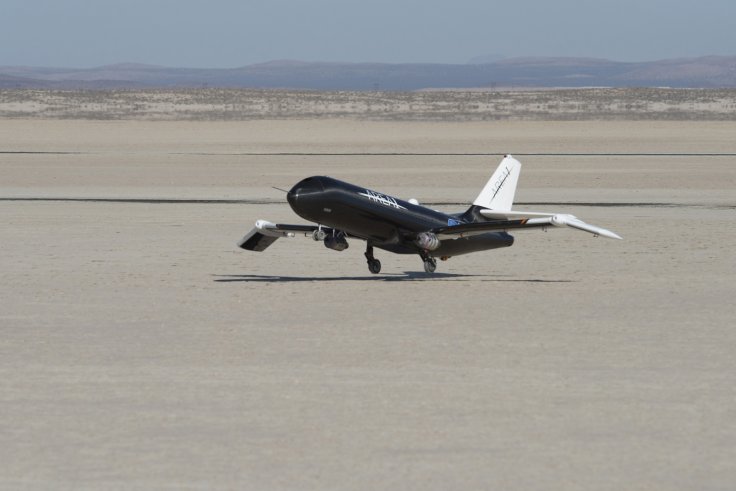
The technology was tested on Prototype Technology-Evaluation Research Aircraft or PTERA designed and developed by Area-I. The company was also involved in design and integration of a shape memory alloy- actuator.
Area- I Chief Executive Officer Dr. Nicholas Alley said, "PTERA was developed as a flying laboratory, and was used in this flight series to host the SAW experiment."